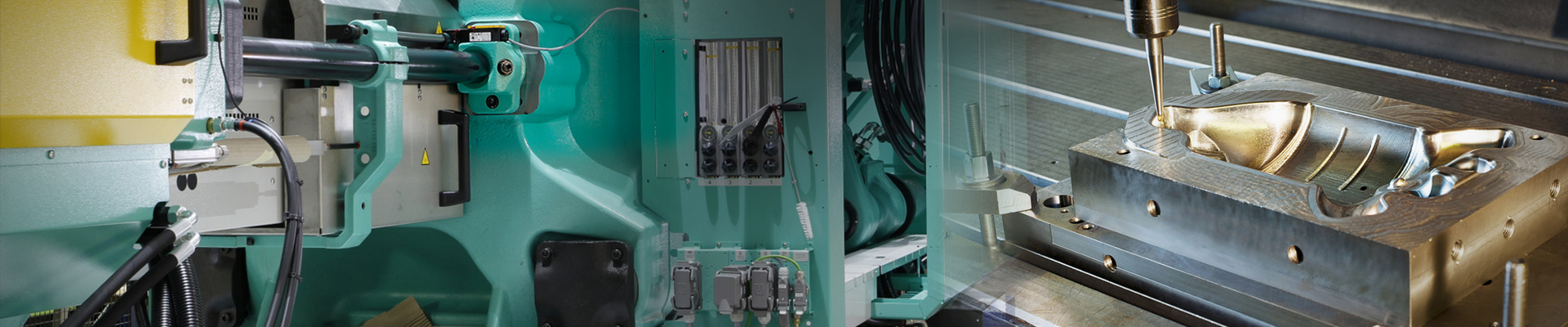
Rotational Molding
We also offer manufacturing solutions by rotational molding
Rotational molding (rotomolding) and injection molding are two distinct plastic manufacturing processes, each with its advantages and best-use scenarios. Here’s a comparison of when rotational molding is more suitable than injection molding:
When Rotational Molding is More Suitable
- Large, Hollow Parts
- Design Suitability: Rotomolding is ideal for producing large, hollow parts such as tanks, containers, kayaks, and playground equipment. Injection molding struggles with large, hollow parts due to limitations in mold design and the need for complex core mechanisms.Insulation can also be added in the wall.
- Low Production Volumes
- Cost Efficiency: For low to medium production volumes, rotomolding is more cost-effective because it uses less expensive molds made from aluminum or steel. Injection molding requires high-cost, precision-engineered molds, making it less economical for small runs.
- Complex, Seamless Shapes
- Uniform Wall Thickness: Rotomolding naturally produces parts with uniform wall thickness and seamless construction, which is beneficial for parts that need to hold fluids or maintain structural integrity without weak points.
- Durability and Strength
- Material Distribution: The slow rotation of the mold in rotomolding ensures even distribution of material, leading to durable, stress-free parts. This is advantageous for parts that require high impact resistance and longevity.
- Variety of Material Options
- Material Flexibility: Rotomolding can use a wide range of thermoplastics, including polyethylene (PE), polypropylene (PP), and polyvinyl chloride (PVC). These materials often have additives for UV stability, chemical resistance, and color customization.
- Thicker Walls
- Increased Thickness: Rotomolding can easily produce parts with thicker walls where needed, which can be difficult and expensive with injection molding.
- Lower Tooling Costs
- Mold Simplicity: The molds used in rotomolding are simpler and cheaper to produce. This makes it a viable option for prototyping and small-batch production.
- Consistent Quality for Large Parts
Large Scale Consistency: Rotomolding maintains consistent quality over large surface areas and complex geometries without the internal stresses and weld lines that can occur in injection molding.
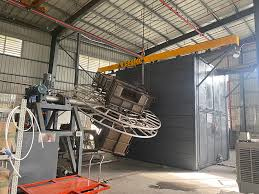
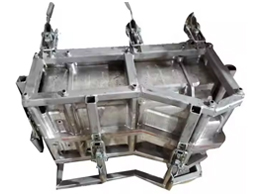
Comparison Table: Rotational Molding vs. Injection Molding
Criteria | Rotational Molding | Injection Molding |
Part Size | Large, hollow parts | Small to medium-sized parts |
Production Volume | Low to medium volumes | High volumes |
Tooling Cost | Lower | Higher |
Part Complexity | Seamless, complex shapes with uniform thickness | Detailed, complex shapes with various thicknesses |
Wall Thickness | Uniform, can be thicker | Varies, generally thinner |
Material Use | Thermoplastics, especially PE, PP, PVC | Wide range of thermoplastics, including engineered resins |
Cycle Time | Longer | Shorter |
Surface Finish | Good, with textures achievable | Excellent, with fine details and smooth finishes |
Mechanical Properties | High durability and impact resistance | High precision and strength |
Cost Efficiency | Cost-effective for large parts and low volumes | Cost-effective for high volumes |
When to Choose Rotational Molding
- Producing large, hollow itemslike tanks, kayaks, and playground equipment.
- When the project requires low to medium production volumesdue to lower tooling costs.
- For parts needing uniform wall thicknessand high durability.
- When working with simpler moldsand cost constraints.
- If thicker walls are necessaryfor the application.
- When seamless construction is importantfor structural integrity and fluid containment.
When to Choose Injection Molding
- For small to medium-sized partswith intricate details and high precision.
- When high production volumesare needed to justify the higher tooling costs.
- When parts require fine surface finishesand high aesthetic quality.
- For parts needing tight tolerancesand complex geometries with varying wall thicknesses.
- If faster production cyclesare essential to meet demand.
Rotational molding (rotomolding) utilizes two primary types of molds: aluminum molds (CNC machined) and welded metal plate molds. Each type has its own advantages, drawbacks, and best-use scenarios.
Aluminum Molds (CNC Machined)
Advantages
- Precision and Detail
- High Accuracy: CNC machining allows for highly precise and detailed mold cavities, which is ideal for producing parts with intricate designs and fine surface finishes.
- Consistency: Ensures consistent part quality across multiple production runs.
- Heat Conductivity
- Efficient Heating and Cooling: Aluminum’s excellent thermal conductivity ensures uniform heating and cooling of the mold, leading to consistent material flow and even wall thickness.
- Lightweight
- Ease of Handling: Aluminum molds are lighter than steel molds, making them easier to handle, install, and changeover during production.
- Corrosion Resistance
- Durability: Aluminum is naturally resistant to corrosion, which enhances the mold’s longevity, especially when working with certain polymers or in humid environments.
Drawbacks
- Cost
- Higher Initial Cost: CNC machined aluminum molds are generally more expensive to produce than welded metal plate molds due to the precision machining required.
- Durability
- Wear and Tear: While durable, aluminum molds are less resistant to wear and impact than steel molds, which may lead to more frequent maintenance or replacement in high-volume production.
Welded Metal Plate Molds
Advantages
- Cost-Effective
- Lower Initial Investment: Welded metal plate molds are generally less expensive to produce than CNC machined aluminum molds, making them suitable for lower budget projects and prototyping.
- Robustness
- Durability: Welded metal plate molds, typically made from steel, are more resistant to wear and impact, making them suitable for high-volume production and rugged applications.
- Customization
- Flexibility in Design: Easier to modify or repair, welded metal plate molds offer greater flexibility for design changes and adjustments during the prototyping phase.
Drawbacks
- Lower Precision
- Surface Finish: Welded metal plate molds do not achieve the same level of detail and smooth surface finish as CNC machined aluminum molds. They may produce parts with rougher surfaces and less precise details.
- Weight
- Handling Difficulty: Steel molds are heavier than aluminum molds, making them more difficult to handle and requiring more robust machinery for installation and operation.
- Thermal Conductivity
- Inefficient Heating and Cooling: Steel has lower thermal conductivity than aluminum, leading to longer heating and cooling times, which can affect cycle times and part consistency.
Comparison Table: Aluminum Molds vs. Welded Metal Plate Molds
Criteria | Aluminum Molds (CNC Machined) | Welded Metal Plate Molds |
Precision and Detail | High, suitable for intricate designs | Moderate, less suitable for fine details |
Heat Conductivity | Excellent, uniform heating/cooling | Moderate, longer heating/cooling times |
Weight | Lightweight, easy to handle | Heavy, difficult to handle |
Durability | Good, corrosion-resistant | Excellent, highly durable |
Cost | Higher initial cost | Lower initial cost |
Surface Finish | Smooth, high-quality finishes | Rougher finishes |
Customization | Limited, harder to modify | High, easier to modify and repair |
Application Suitability | Detailed, high-quality parts | Prototyping, rugged applications |
Maintenance | Less frequent but more costly | More frequent but easier and cheaper |
When to Use Each Type
Aluminum Molds (CNC Machined)
- High Precision Requirements: Ideal for parts requiring fine details, intricate designs, and smooth surface finishes.
- Consistent Quality: Suitable for applications where uniformity and part consistency are critical.
- Corrosion Resistance: Beneficial in environments prone to moisture or when working with certain polymers.
Welded Metal Plate Molds
- Cost Efficiency: Best for projects with limited budgets or lower production volumes.
- Durability: Suitable for high-volume production and parts that need to withstand rugged use.
- Prototyping and Customization: Ideal for prototyping and projects requiring frequent design modifications or adjustments.
By understanding the strengths and limitations of each process, manufacturers can select the most suitable molding method for their specific applications, ensuring optimal performance, cost-efficiency, and product quality.