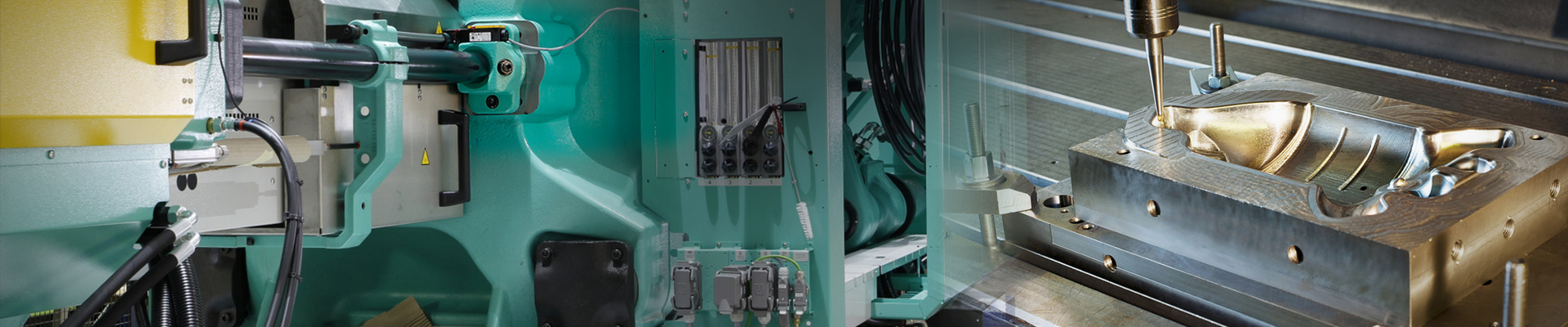
When Blow Molding is More Suitable
We also offer manufacturing solutions by blow molding.
- Hollow Parts
- Design Suitability: Blow molding is ideal for producing hollow parts such as bottles, tanks, and containers. Injection molding is less efficient for hollow parts due to the complexity of mold design and core mechanisms required.
- Large Parts with Uniform Wall Thickness
- Consistency: Blow molding is suitable for large parts that need uniform wall thickness, such as fuel tanks, large storage containers, and automotive ductwork. Injection molding may struggle with maintaining uniform wall thickness in large parts.
- High Production Volumes
- Efficiency: Blow molding is cost-effective for high-volume production runs of hollow parts. The process allows for quick production cycles and high output rates.
Less-Known Applications
- Chair Backs and Seats
- Ergonomic Designs: Blow molding can produce ergonomic chair backs and seats with complex curves and hollow structures, providing both comfort and strength while reducing weight.
- Cost-Effectiveness: For large quantities, blow molding can be more economical than injection molding, especially for parts with a hollow design.
- Sporting Goods
- Kayaks and Canoes: Blow molding is used to produce large, hollow sporting goods such as kayaks and canoes, providing durability and buoyancy.
- Balls and Play Equipment: Hollow balls and playground equipment can be efficiently produced using blow molding.
- Household Items
- Coolers and Storage Containers: Blow molding is suitable for making durable, insulated coolers and large storage containers.
- Watering Cans and Laundry Hampers: These items benefit from the lightweight and durable properties of blow-molded plastic.
- Industrial Products
- Tool Cases and Equipment Housings: Blow molding can produce robust, impact-resistant cases and housings for tools and equipment.
Traffic Cones and Barriers: These safety products are often blow molded for their durability and hollow structure.
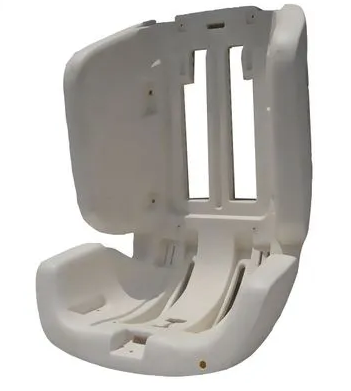
Comparison Table: Blow Molding vs. Injection Molding
Criteria | Blow Molding | Injection Molding |
Part Type | Hollow parts (bottles, tanks, containers) | Solid parts or complex geometries with inserts |
Production Volume | High volumes | High volumes |
Tooling Cost | Lower for large hollow parts | Higher due to complex molds |
Part Complexity | Hollow shapes with internal geometries | Intricate designs with fine details |
Wall Thickness | Uniform | Variable, can be thin or thick |
Material Use | Variety of thermoplastics | Wide range of thermoplastics, including engineered resins |
Cycle Time | Quick for hollow parts | Shorter for solid parts |
Surface Finish | Good, but less detailed | Excellent, with fine details and smooth finishes |
Mechanical Properties | Good impact resistance and durability | High precision and strength |
Cost Efficiency | Cost-effective for hollow parts and high volumes | Cost-effective for complex geometries and high volumes |
Initial Investment | Lower for blow molds | Higher for injection molds |
Design Flexibility | Suitable for large, hollow shapes | Suitable for intricate designs and solid parts |
Turnaround Time | Fast for high-volume hollow parts | Moderate, depending on complexity |
When to Choose Blow Molding
- Producing hollow partssuch as bottles, tanks, and containers.
- For large, uniform wall thickness partssuch as automotive ducts and fuel tanks.
- When high production volumesare needed for hollow parts.
- For complex, hollow shapesthat are challenging for injection molding.
- When weight reductionand material efficiency are important, as in automotive parts.
- Durability and impact resistanceare required for the end-use application.
When to Choose Injection Molding
- For small to medium-sized solid partswith intricate details and high precision.
- When high production volumesare needed to justify the higher tooling costs.
- When parts require fine surface finishesand high aesthetic quality.
- For parts needing tight tolerancesand complex geometries with varying wall thicknesses.
- If faster production cyclesare essential to meet demand.
- High strength and mechanical propertiesare required for the end-use application.