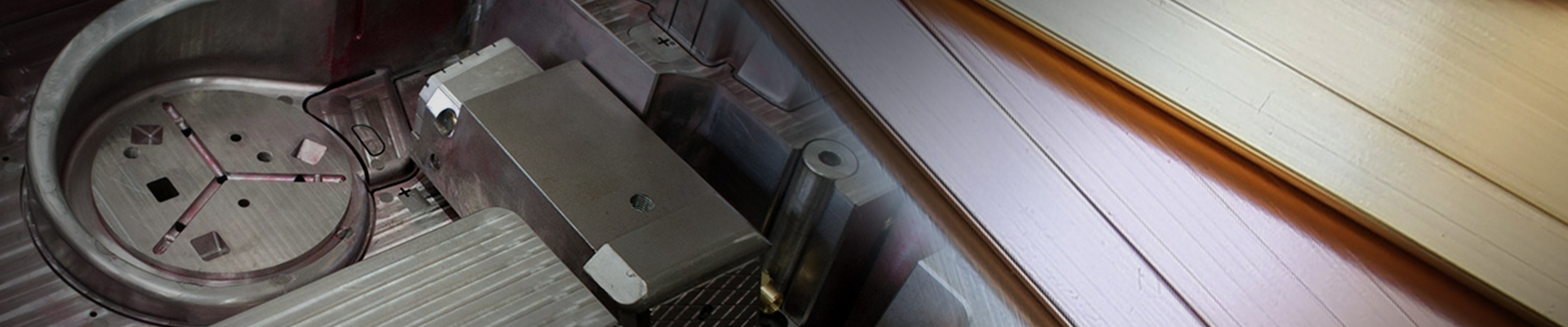
Machine Tonnage required to make a part will affect the unit production cost and production speed.
Calculation Steps
- Determine the Projected Area: The projected area is the area of the part as seen from the direction of the clamping force. This includes any runners and sprues.
Projected Area (A)=Length×Width
- Determine the Injection Pressure: The injection pressure varies depending on the material and part design. Typical values range from 2,000 to 20,000 psi (pounds per square inch) or 140 to 1,400 bar.
- Calculate the Clamping Force: Multiply the projected area by the injection pressure to get the clamping force.
Clamping Force (F)=Projected Area (A)×Injection Pressure (P)
- Convert to Tonnage: Convert the clamping force from pounds to tons (1 ton = 2,000 pounds).
Tonnage Required=Clamping Force (F) in pounds \ 2,000
Simplified Tonnage Table
Below is a simplified table showing the required tonnage for various projected areas and injection pressures. This table assumes the most commonly used injection pressures.
Projected Area (sq in) | 2,000 psi (tons) | 5,000 psi (tons) | 10,000 psi (tons) | 15,000 psi (tons) | 20,000 psi (tons) |
10 | 10 | 25 | 50 | 75 | 100 |
20 | 20 | 50 | 100 | 150 | 200 |
30 | 30 | 75 | 150 | 225 | 300 |
40 | 40 | 100 | 200 | 300 | 400 |
50 | 50 | 125 | 250 | 375 | 500 |
60 | 60 | 150 | 300 | 450 | 600 |
70 | 70 | 175 | 350 | 525 | 700 |
80 | 80 | 200 | 400 | 600 | 800 |
90 | 90 | 225 | 450 | 675 | 900 |
100 | 100 | 250 | 500 | 750 | 1,000 |
Notes
- Material and Part Design: The actual injection pressure can vary based on the material used and the complexity of the part design. Consult material data sheets and perform mold flow analysis for precise calculations.
- Safety Factor: It’s advisable to add a safety factor (typically 10-20%) to the calculated tonnage to account for variations in the molding process and ensure consistent part quality.
By using these steps and the reference table, you can estimate the tonnage required for your injection molding machine to produce high-quality plastic parts.